Marginal Costing And Absorption Costing
Business climate is changing rapidly in current scenario therefore management needs every day and accurate information about the business and costs incurred to take wise decisions to avoid all possible wastages and losses and to augment the effectiveness of the business. The management must to make proper assessment of the productivity and performance of the personnel only if it uses effective costing methods. It is recommended to consider a particular costing method because costing methods that a business adopts can play vital roles in the development of advanced manufacturing technologies and business philosophies. Marginal costing and absorption costing are the basic two methods of costing that are used for managerial decision making. Both are types of product costing systems. Absorption or full costing includes direct materials, direct labour and both variable and fixed manufacturing overhead in the product costs whereas variable costing does not include manufacturing fixed costs along with direct material and direct labour (Weygandt, Keiso and Kimmel, 2005, p. 265). Marginal costing is the elementary tool that helps management in taking most appropriate decisions and understands accurate cost structures.
Marginal Costing: Basic principles-Marginal costing is described in literature as ascertaining of marginal cost and of the effect on profit on changes in volume type of output by differentiating between fixed and variable cost. Marginal cost is the volume of any given volume of output by which aggregate variable costs are changed if the volume of output is increased by one unit. Practically, it is measured by total variable cost attributable to one unit. Marginal cost can precisely be the sum of prime cost and variable overhead.

Under marginal costing, variable costs are attributed to cost units for a fixed period and fixed costs are written off in full against the total contribution (Lucey and Lucey, 2002). Nigam, Nigam and Jain (2004) defined marginal costing as the costing technique that "charges only the variable costs to the cost units" (p. 398). CIMA terminology of marginal costing defined that "it is a principle where by variable costs are charged to the cost units and fixed costs attributable to the relevant period is written off in full against the contribution of that period" (Bhattacharyya 2005,). Cost of a unit consists only of out of pocket costs that are direct, variable or avoidable costs. These costs are incurred only if specific products are manufactured and sold. Marginal costing considers cost behaviour. Costs are variable or fixed, but, marginal costing takes in to account only variable costing (Bendrey, Hussey and West, 2003). Marginal cost is variable costs attributed to the production costs because it varies according to the changes in the production as well as final output. When one extra unit of the product is manufactured, the extra cost incurred for the manufacturing of that extra unit will always be variable because the fixed costs are constant. Marginal costing is a vital management accounting practice that is used to provide managerial information about profit and volume relationship and costs incurred in the business. Marginal costing facilitates effective managerial decision making, valuation, cost control and monitoring and profit planning etc (Glautier and Underdown, 2001).
Figure: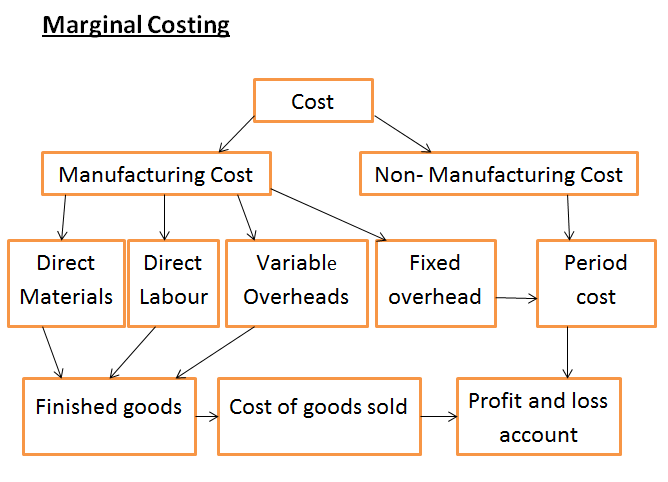
Salient features of Marginal Costing
Marginal costing involves determining marginal costs. Since marginal costs are direct cost, this costing technique is also known as direct costing. In marginal costing, fixed costs are never charged to production. They are treated as period charge and is written off to the profit and loss account in the period incurred. Once marginal cost is determined, contribution can be computed. Contribution is the excess of revenue over marginal costs. The marginal cost statement is the basic document/format to capture the marginal costs. It is a procedure of recording costs and reporting profits. All operating costs are differentiated into fixed and variable costs. Main characteristics of marginal costing are as follows:
- All elements of costs are categorized into fixed and variable components. Semi variable costs are also analysed into fixed and variable elements.
- Marginal or variable costs such as direct material, direct labour and variable factory overheads are treated as the cost of the product.
- Under marginal costing, the value of finished goods and work in process is also comprised only of marginal costs. Variable selling and distributions are excluded for valuing these inventories. Fixed costs are not considered for valuation of closing stock of finished goods and closing WIP.
- Fixed costs are treated as period cost and is charged to profit and loss account for the period for which they are incurred.
- Prices are determined with reference to marginal cost and contribution margin.
- Profitability of departments and products is determined with reference to their contribution margin.
Advantages of Marginal Costing
Marginal Costing is simple to understand variable versus fixed cost concept. A useful short term survival costing technique particularly in competitive environment or recessions where orders are accepted as long as it covers the marginal cost of the business and the excess over the marginal cost contributes toward fixed costs so that losses are kept to a minimum. Marginal Costing shows the relationship between cost, price and volume. It provides better information hence is a useful managerial decision making tool. Marginal Costing concentrates on the controllable aspects of business by separating fixed and variable costs. Marginal costing is constant in nature. It remains the same per unit of product irrespective of the volume of production. It has realistic valuation and it facilitates cost control (Prasad and Sinha, 1990).
Disadvantages of Marginal Costing
Marginal cost has many drawbacks since it makes use of historical data while decisions by management relates to future events. Marginal cost ignores fixed costs to products as if they are not important to production. Marginal costing fails to recognize that in the long run, fixed costs may become variable and its oversimplified costs into fixed and variable as if it is so simply to demarcate them. It is not effective costing technique in the long run for pricing decision as it ignores fixed cost. Marginal costing has very limited scope (Prasad and Sinha, 1990)
Application of marginal costing: Marginal costing has various applications.
First application is to take Managerial Decision Relating to Determination of Optimum Selling Price. To determine the optimum selling price of any product or service is major challenge for a manager of any company because company wants to make profit of each unit of any product or service. In marginal costing technique, fixed cost will not be changed at any level of production. Only variable cost is changed for getting optimum selling price where company can achieve expected profit.
Secondly, Marginal costing is applied to check the Effect of Reducing of Current Price on profit.
Other application of Marginal costing is to choose of Good Product Mix. It may be possible that company is producing more than one product, at that time company has to calculate each product's contribution margin or gross profit margin. After this, manager checks which product is giving high contribution to margin. Company manager will give preference to that product whose contribution is high. One more decision can be taken by manger. He can check contribution by producing different quantity of different products. If he sees any quantity of products is producing maximum contribution, it will be equilibrium point. Production of units at that quantity will be benefited to company.
Marginal costing is also applied for calculation of Margin of Safety. Marginal costing can be utilized for calculating margin of safety. Margin of safety is difference between actual sale and sale at breakeven point.
Lastly, Marginal costing assists in decision regarding to sell goods at different prices to different customers. Sometime, company has to give special discount to special customers. These customers may be government, foreign companies or wholesaler. At that time manager has to take decision at what limit, we can give discount to special customers. Marginal costing may help in this decision.
It is established from management literature that Marginal costing is useful procedure in managerial decision making. Management's production and cost and sales decisions may be easily affected from marginal costing. Therefore, it is the part of cost control method of costing accounting.
Absorption costing: Absorption costing is an effective costing methods in which all manufacturing costs including both variable and fixed costs are attributed to the production costs. Absorption costing is also known as full costing which absorbs or recovers both fixed and variable costs. The cost of a unit is taken as variable cost per unit plus an allocated share of the fixed overheads (Jawahar-Lal, 2008). Direct costs are directly ascribed to the cost units. Manufacturing overhead costs are attributed to the product and other overheads. Variable costs such as direct material cost and direct labour cost are directly attributed to the product while fixed costs are charged over different products that the company manufactured over a specified period of time (Williams, Haka and Bettner, 2004).
In management accounting literature, absorption costing is defined as practice of charging costs both variable and fixed to operations, products and processes (CIMA). In the technique of absorption costing, prices are the functions of the costs and therefore demand of the product is never considered. It comprises of past costs that may not be relevant to the prevailing decision making and pricing processes. Some management experts criticized that absorption costing may not be able to provide precise information for decision making in today's highly vibrant and complex business environments (Boardguess, 2009). Under absorption costing, all overhead costs are absorbed to a particular product along with direct costs. Theorists define absorption costing as a technique that is required for the external reporting purposes (Broadbent, Broadbent and Cullen, 2003).
Absorption costing: A simplified view of Production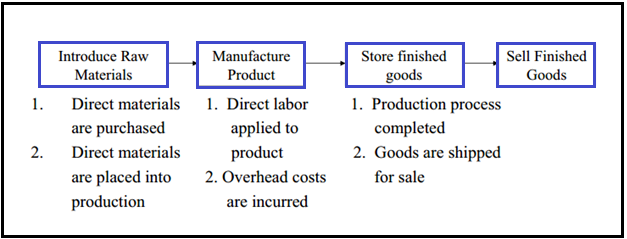
Components: Following are the Absorption Costing Components.
Direct materials: Those materials that is included in a finished product.
Direct labour: The factory labour costs required to construct a product.
Variable manufacturing overhead: The costs to operate a manufacturing facility which varies with production volume. Examples are supplies and electricity for production equipment.
Fixed manufacturing overhead. The costs to operate a manufacturing facility, which do not vary with production volume. Examples are rent and insurance.
There are three different types of Absorption Costing System
- Job Order Costing: In Job Order, Costing costs are assigned to the product in Batches or lots such as Printing, Furniture manufacturing, Bicycle Manufacturing.
- Process Costing: In Process Costing, costs are systematically assigned to the product, since there are no discreet batches to assign costs. Such as Oil Distilling, Soda Manufacturing etc.
- ABC Costing: ABC Costing assigns cost from cost centres to the product. It is best suited in a multi-product firm, where there are different volumes.
There are following features of absorption costing (Debarshi, 2011):
- In this procedure, both fixed as well as variable costs are allocated to the cost unit.
- The overhead cost is allocated to cost unit with the help of overhead absorption rate.
- In this process, closing inventories are also valued at both fixed as well as variable costs.
- Under this technique, the periodic profit is affected by a change in inventory as well as in the volume of sales. Accordingly the profit may be shifted from one accounting period to another by increasing or decreasing the inventories.
- In this process, profit becomes the function of production instead of sales.
Absorption Costing Procedure
- Allocation: There is a collection of cost by type and allocation of as much cost as possible directly to cost centres.
- Apportionment: Overhead that cannot be allocated to specific cost centres are spread between cost centres on a fair basis. In next stage, there is re-apportionment of cost centre overhead to production cost centres. Methods of re-apportionment are direct and step down method. Direct method of re-apportionment involves apportioning the costs of each service cost centre to production cost centres only. Step-down method of re-apportionment recognises the inter-service cost centre work. Each service cost centre's costs are not only apportioned to production departments but to some (but not all) of the other service cost centres that makes use of the service provided
- Absorption: It involves identifying the absorption base, establishing an absorption rate for each production cost centre and absorption of overheads into cost centre.
Benefits: Absorption costing provides an advantage when company do not sell all of its manufactured products during the accounting period. Company may have finished goods in inventory. Because management assign a per-unit amount for fixed expenses, each product in inventory has a value that includes part of the fixed overhead. Company do not show the expense until it actually sells the items in inventory. This can improve profits for the period. Absorption costing reduces the work burden of segregation of cost into fixed and variable parts. It confirms the accrual concepts by matching the cost with the revenue for a particular period (Debarshi, 2011).
Drawbacks: Absorption costing can be effectively used only at a constant level of output to get a uniform unit cost. Under this technique, unit cost would be different at different levels of output (Debarshi, 2011). Absorption costing can artificially inflate profit figures in any given accounting period. Because managers will not deduct all of fixed overhead if they have not sold all of their manufactured products, their profit-and-loss statement does not show the full expenses they had for the period. This can mislead them when they will evaluate profitability.
Comparison Marginal Costing of Absorption Costing
Marginal costing method is applied since long time by many businesses and it is more convenient and easy to adopt in the business. As it is variable costing technique, chances of over absorption or under absorption are comparatively less. Marginal costing avoids apportionments that are made on arbitrary basis. It is more appropriate for managerial decision-making and controlling processes. Closing inventory is easily valued under marginal costing. When comparing marginal costing to absorption costing, it is established that absorption costing often encourages over production because there is a chance that the reported profit can be increased by the increase of inventory levels. It is argued that fixed costs are never variable in the long term. Davies and Pain (2002) argued that there are numerous alternative bases of overhead allocation and attribution that may characterise different interpretation too. Fixed costs are some time under absorbed when a specific manufacturing activity is not equal or not greater than the budgeted level.
When evaluating Absorption Costing, it is determined that Closing stock values include a proportion of fixed production overhead and therefore absorption costing meets the international accounting standard. The costing method of absorption or full costing is reasonable in the accounting view point because fixed manufacturing costs are incurred for manufacturing an output. Absorption costing practise is considered as more accurate because a particular share of the production costs are apportioned against future sales.
Differences between absorption costing and Marginal Costing
The main difference is Inventory Valuation. Absorption costing includes overheads, except marketing so that the inventory value represents all the costs of getting inventory to its current condition and location. But, marginal costing eliminates fixed overheads for stock valuation and it thus doesn't represent full costs of manufacturing the goods (Nigam, Nigam and Jain, 2004,). It demonstrates that both absorption and marginal costing influence the valuation of inventory in different levels. In marginal costing technique, inventories are valued in the basis of variable production costs and therefore the stock value is relatively in a lower level. The absorption costing considers fixed factory overhead and hence value of inventory will be relatively higher than that in absorption costing (Jawahar-Lal, 2008).
Another difference in both techniques is cost elements of product cost. The selling and administrative expenses, let it be fixed or variable nature, are measured as period costs and these are not considered as product costs in both absorption and marginal costing methods. But, fixed factory overhead is treated completely different in both absorption and marginal costing methods. Fixed overheads are brought in to all calculations on the assumption that they are to be recovered. But in marginal costing, fixed overheads are considered irrelevant for short run decisions (Jawahar-Lal, 2008).
There is also difference in Jobs and Products in both techniques. Marginal costing is visualized as more realistic as compared to the method of absorption costing. Marginal costing considers only those costs that are easily attributable and identifiable to the job or a product (Chadwick, 1993). Marginal costing is more appropriate, reliable and correct with internal financial reporting, whereas absorption costing is most suitable for external financial reporting and analysis.
There is also difference in both methods with reference to Net-income. Fixed overheads are treated differently in marginal costing and absorption costing and therefore it is obvious that the net income result in both of these costing tools will certainly be different as well. Suitability for decision making absorption costing cannot be used because the costs that it takes in to account are imprecise in nature. Usually, marginal costing is extensively suggested for managerial decision making as the costs that it considers are observable to a particular product and hence it is useful for managerial decision making.
Distinction between marginal and absorption costing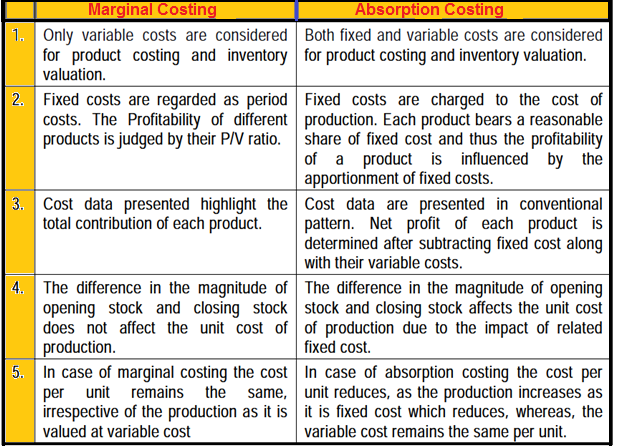
To summarize, Absorption and marginal costing are fundamentally different in terms of treating the overheads, inventory valuation, appropriateness for decision-making, net income and methods of calculation. Marginal costing is a technique where only variable cost or direct cost will be charged to the cost unit produced. Marginal costing also demonstrations the effect on profit of changes in volume or type of output by differentiating between fixed and variable costs. Absorption costing is a technique for appraising or valuing a firm's total inventory by including all manufacturing costs as product costs, regardless of whether they are variable or fixed.