Material Requirement Planning
Material requirement planning is a system based approach, which organizes all necessary production material. Material Requirements Planning, abbreviated as MRP is a straightforward system to calculate arithmetically the requirements of the input materials at different points of time based on actual production plan. Theorists described MRP as a planning and scheduling system to meet time-phased materials requirements for production operations. It is a set of techniques that calculate the requirement of all items structured in bill of material. The calculated requirements are based on the quantity and timing requirement of end items listed in master production schedule. The item calculation requirement is based on the master production schedule, the bill of material file and the item master file (Toomey, 1996). The main intent of is to meet the delivery schedule of finished products as specified in the master production schedule. MRP is a material planning method that developed in the decade of1970 that utilized computer technology.
Material requirement planning is an information system for production planning based on inventory management. It is stated in management studies that Information Technology has major role in designing and implementing Material Requirements Planning systems and processes as it provides information about manufacturing needs as well as information about inventory levels. MRP techniques focus on optimizing inventory. MRP techniques are used to explode bills of material, to calculate net material requirements and plan future production. The main traits of MRP are the creation of material requirements via exploding the bills of material, and time-phasing of requirements using posted average lead times. MRP II was developed as the second generation of MRP and it features the closed loop system: production planning drives the master schedule which drives the material plan which is the input to the capacity plan. Feedback loops provide input to the upper levels as a reiterative process.
The vital components of material planning include the following:
- Material planning provides information that all the required raw material and products are available for production.
- Material planning guarantees that inventory level is maintained at its minimum levels. But also ensures that material and product are available whenever production is scheduled, therefore, helping in matching demand and supply.
- Material planning provides information of production planning and scheduling but also provides information around dispatch and stocking.
The major objectives of MRP: The goal of the Material Requirements Planning document is to supply information that will facilitate the company to have enough inventory on hand to fulfil demand, available only when needed at a quality level that meets specification, (and at the lowest price. A good Material Requirements Planning program can offer the fundamental needs of keeping inventory levels low and fulfilling customer expectations for on time delivery. Major objectives are as under:
- Reduction in Inventory Cost: MRP offers accurate quantity of material at right time to meet master production schedule to avoid the cost of excessive inventory.
- Meeting Delivery Schedule: By minimizing the delays in materials procurement, production decision making, MRP assists evade delays in production thereby meeting delivery schedules more consistently.
- Improved Performance: By stream lining the production operations and minimizing the unplanned interruptions, MRP focuses on having all components available at right place in right quantity at right time.
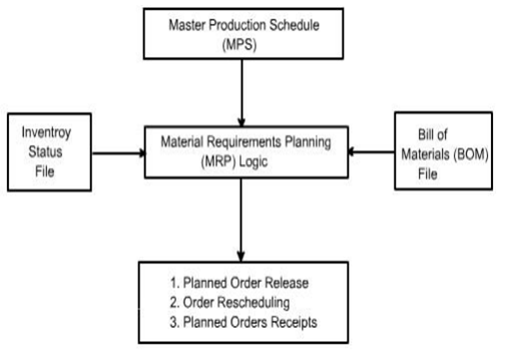
Master Production Schedule: MPS is designed to fulfil the market demand that include company orders and forecasted demand in future in the taken planning horizon. MPS mainly represents the complete delivery schedule of the end products. However, orders for replacement components can also be included in it to make it more comprehensive.
Bill of Materials File: This symbolizes the product structure. It includes information about all sub components needed, their quantity, and their sequence of develop in the end product. Information about the work centres performing build-up operations is also included in it (Toomey, 1996).
Inventory Status File: Inventory status file maintains recent record of each item in the inventory. Information such as, item identification number, quantity on hand, safety stock level, quantity already allocated and the procurement lead time of each item is recorded in this file.
After getting input from these sources, MRP logic processes the available information and gives information about the following:
Planned Orders Receipts: This is the order quantity of an item that is planned to be ordered so that it is received at the beginning of the period under consideration to meet the net requirements of that period. This order has not yet been placed and will be placed in future.
Planned Order Release: This is the order quantity of an item that is planned to be ordered in the planned time period for this order that will ensure that the item is received when needed. Planned order release is determined by offsetting the planned order receipt by procurement lead time of that item.
Order Rescheduling: This emphasizes the need of any expediting, de-expediting, and cancellation of open orders etc. in case of unexpected situations.
Basic steps in Material requirement planning are as follows:
- Identifying requirement.
- Running MRP- creating the suggestion.
- Firming the suggestion.
Material Requirements Planning solution consist of modules for inventory management, product definition and costing, master scheduling and materials requirement planning, capacity planning, work order management, purchase order management, sales order management, shipping and receiving, and sales analysis. Material requirements planning software can also include a full accounting package, if desired.
Advantages of MRP: Material requirement planning is framework to give valuable information for decision makers. Main benefits from any MRP system are the capability of the inventory planner to use the information well. The particular benefits of MRP include the following:
- Increased customer service and satisfaction
- Improved utilization of facilities and personnel
- Better inventory planning and scheduling
- Faster response to market changes and shifts
- Reduced inventory levels without reduced customer service
Major issues of using procedure of Material requirements planning are that they are not fully perfect. If there is some error in the system, then it is going to throw off all the other numbers thus making the outputted data inaccurate. The issue with MRP systems is the integrity of the data. If there are any errors in the inventory data, the bill of materials, that are called 'BOM data, or the master production schedule, then the outputted data will also be incorrect. Data integrity is impacted by imprecise cycle count adjustments, mistakes in receiving input and shipping output, scrap not reported, waste, damage, box count errors, supplier container count errors, production reporting errors, and system issues. Many of these types of errors can be minimized by implementing pull systems and using bar code scanning. Most sellers of this type of system recommend at least 99% data integrity for the system to give valuable results. Another problem is that Material requirements planning systems do not necessarily factor in other warehouses in other cities or states. Therefore, the system will explain that company do not need to order anymore parts when in fact those parts are in other factories. Other major factor is that the MRP system can not consider manpower.
To summarize, material requirements planning is a computer-based inventory management system designed to help production managers in scheduling and placing orders for items of dependent demand. Material Requirements Planning is software based production planning, which utilizes an inventory system to systematize various manufacturing processes. Principally when a company is going to produce products to sell, this software organizes all inventories, while making sure that all the products and materials are in place in order for this to be possible.